CAT Vehicle Students Paving the Way for Self-Driving Cars
Prestigious summer program prepares students for graduate school and to enter an industry projected to generate $300B.
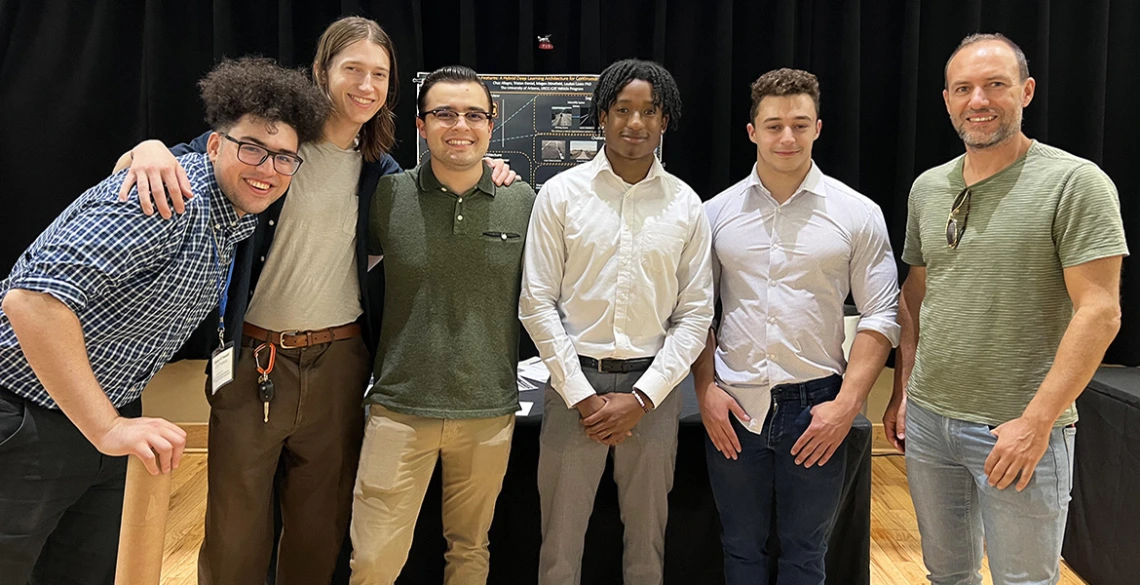
Pictured from left to right are Hasan Al Saeedi, Kyle McIllece, John Dominguez-Trujillo, Tristan Daniel, Chaz Allegra and Loukas Lazos.
A group of engineering students from across the country gathered on the University of Arizona campus this summer to help shape the future of self-driving cars. The students participated in the Cognitive and Autonomous Test Vehicle (CAT) program, researching the intelligence systems, security and reliability of a rapidly developing industry.
The 10-week program is hosted by the Department of Electrical and Computer Engineering and is part of the UA’s Undergraduate Research Opportunities Consortium (UROC), where students from both community colleges and universities work with faculty and graduate students to put scientific concepts to real-world use. CAT was funded through a $415,000 National Science Foundation grant that began in 2020 and extends until 2024.
“The most important skill that the students developed is to apply scientific rigor,” said ECE professor Loukas Lazos, principal investigator of the NSF grant. “We worked on basic elements of research such as conducting literature reviews, problem selection and modeling, composing evaluation criteria, developing multiple candidate solutions, conducting theoretical analysis and experimental validation.”
Each summer, participating students stay on campus, receive a $6,000 stipend, and earn letters of recommendation from faculty members toward their future goals. UROC programs help students pursue graduate education and include elements such as graduate school test workshops. ECE also hosted the UROC program PACT this past summer.
In addition to graduate school preparation, this year’s CAT students appreciated the skills they learned and the camaraderie formed between team members.
Across the 10 weeks, the students developed a deep understanding of intelligent transportation systems, learned how to read technical papers, and honed their communication skills in highly complex settings. The students were split into three groups to research areas such as verifying the veracity of a vehicle-to-vehicle messaging, continuous authentication for vehicle platooning using dynamic traffic, and lane detection.
"I always had an interest in working on issues in autonomous ground vehicles, vehicular security, and machine learning. The projects that were offered allowed for research in all of these areas," said UA mechanical engineering and mathematics major John Dominguez-Trujillo. "With this, you are surrounded by amazing mentors and graduate students that consistently grow your knowledge and colleagues that are just as motivated as you. Given all this support, you are able to grow as a learner, researcher, and individual while building a solid foundation for your future ambitions."
The eight students this year majored in electrical and computer engineering, computer science and mechanical engineering. According to graduate student mentor Ziqi Xu, their perspectives fostered an intellectual atmosphere.
“Collaborating with undergraduate participants who brought diverse backgrounds provided fresh insights and perspectives to my research projects,” Xu said.
CAT and other UROC programs fall under the umbrella of Research Experiences for Undergraduates. These programs are geared toward undergraduate students who may otherwise not have the opportunity to engage with such technical research and rank among the most prestigious summer opportunities of their kind. Previous CAT Vehicle groups have researched traffic light detection for autonomous vehicles, replication of different driving styles, and adaptive cruise control for safe operation in congested traffic.
"The freedom given to us simulated working in an environment where the correct answer is not immediately available and where I have to put in the effort to find it," said Oakton Community College student Hasan Al Saeedi.
All evidence points to the fact that the students are becoming well-versed in a booming and highly skilled market. In 2017, the Brookings Institute estimated that $80 billion had been invested in the self-driving technology industry. However, McKinsey & Company consulting firm predicts that the global industry could create more than $300 billion in revenue by 2035.
“The CAT Vehicle REU program is an excellent opportunity for undergraduates to experience the rush of scientific discovery and achievement,” Lazos said. “The students who complete the program return to their home institutions with a strong focus on aligning their learning with the great challenges faced by our society and a passion to solve them.”