Working With Local High-Tech Firms Creates Revenue Stream and Strong Industry Reputation for UA Engineering Lab
Small-scale fabrication at the UA leads to large-scale funding by industry.
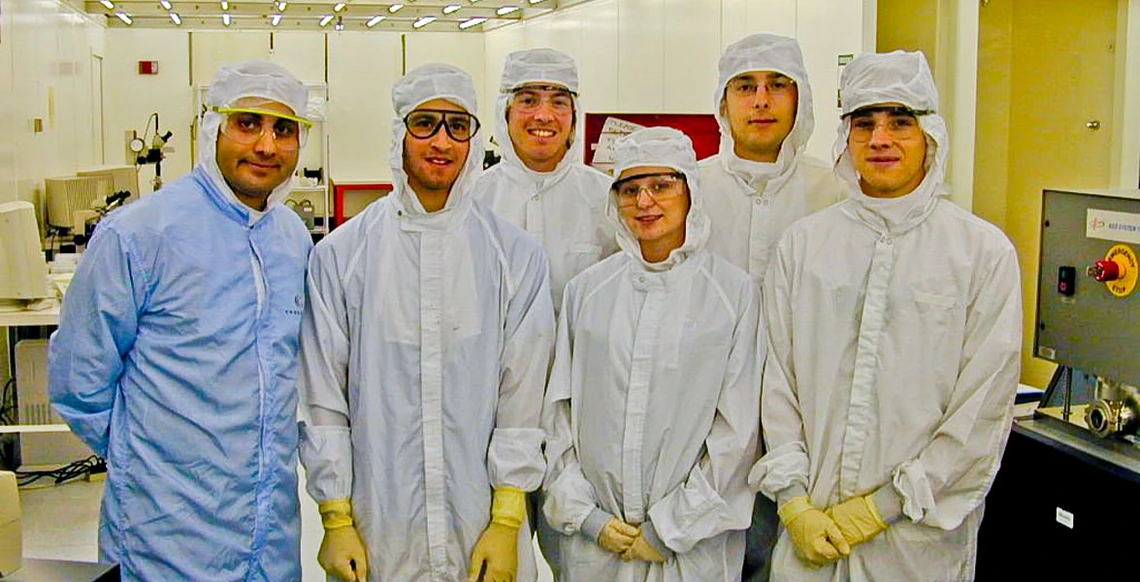
Facility supervisor Omid Mahdavi, left, and a group of materials science and engineering students who use the lab as part of their course in microfabrication.
Tiny high-tech devices are big news for local industry at the University of Arizona Micro/Nano Fabrication Center.
The center provides commercial clients with prototyping services, clean room facilities and semiconductor chip fabrication equipment to develop new products, said Omid Mahdavi, facility supervisor.
Tucson-based Tempronics Inc., which recently raised $2.7 million in venture capital, used the Micro/Nano Fabrication Center to prototype and test new devices designed to convert waste heat into electricity, said Tarek Makansi, Tempronics CEO.
"When materials are made with features at nanometer dimensions, their physical properties change, and these new properties can be exploited for better performing products," Makansi said. "In our case, we are using nanometer properties of materials to make efficient thermoelectric devices for cooling and conversion of heat to electricity."
For example, up to 75 percent of the energy produced by internal combustion engines is wasted as heat. By converting waste heat into electricity, Tempronics' devices could double the mileage of hybrid electric cars, or provide additional power to automotive electrical systems in conventional vehicles.
The firm's thermo-tunneling effect technology devices use two stacks of proprietary thin films separated by a tiny nano-gap. One side of the device is hot and the other side is cold, with the hot side converting heat into electrons that cross the gap to the cooler side, Mahdavi said.
"It's a nano-gap device that is designed to allow the heat to be converted back into electrical current," Mahdavi said. "These are the type of devices that you would put on an engine, or a refrigeration unit, or a solar panel to capture the waste heat and reconvert that back to an electrical current, thereby improving the efficiency of the device."
Other MNFC clients include Araca Inc., a UA spinoff what works in chemical and mechanical polishing of silicon substrates, and Climax Engineered Materials, a mining operation, Mahdavi said.
Revenue from the center's clients totals approximately $130,000 per year, which covers about half of MNFC's salaries and operational costs, he said.
The number of staff at the center -- currently 2.1 FTEs -- limits the amount of commercial work that can be accepted, said Mahdavi. Funding for more staff and some needed equipment could increase the number of clients the facility serves, and bump up revenues with a goal of making the operation self-sustaining, he said.
Industry-University Collaboration
Providing good service and forging strong relations with clients like Tempronics have helped growth.
"It has been very symbiotic. We have benefitted as much as they have benefitted from this relationship. We have been exposed to a number of other industrial clients that came to check up on Tempronics' operations here," Mahdavi said. "Tempronics has put in a good word for the university and the type of service they are getting here. It is always good to have a business here that can vouch for your quality, and that is what Tempronics has done."
"Our collaboration with companies allows them to keep their intellectual property. We sign nondisclosure agreements with the company," he said. " A critical component of this relationship is making sure their IP remains their IP."
The 15,000-square-foot center, located adjacent to the Electrical and Computer Engineering building, also provides a campus-wide resource for research and education, Mahdavi said.
MNFC's high-capacity ultrapure water deionization plant provides 18 Mohm water to researchers across campus, and numerous UA researchers use the center's services, Mahdavi said. Services include photolithography, plasma etch and clean, chemical mechanical planarization, thermal oxidation and annealing, metallization, and metrology. MNFC also works in cooperation with other labs on campus that have devices the center may lack.
Students on courses in semiconductor manufacturing, electromechanical system manufacturing, and electrical and computer engineering also use the site, Mahdavi said. "We are an integral part of the engineering aspects of making these devices in these courses," he said. There are at least three or four courses that rely on our services to educate their students."