UArizona Machine Set to 3D-Print Jet Engine Parts
A $400K piece of equipment provided by Honeywell expands University of Arizona’s additive manufacturing initiative with its ability to print metal components for aerospace and medical needs.
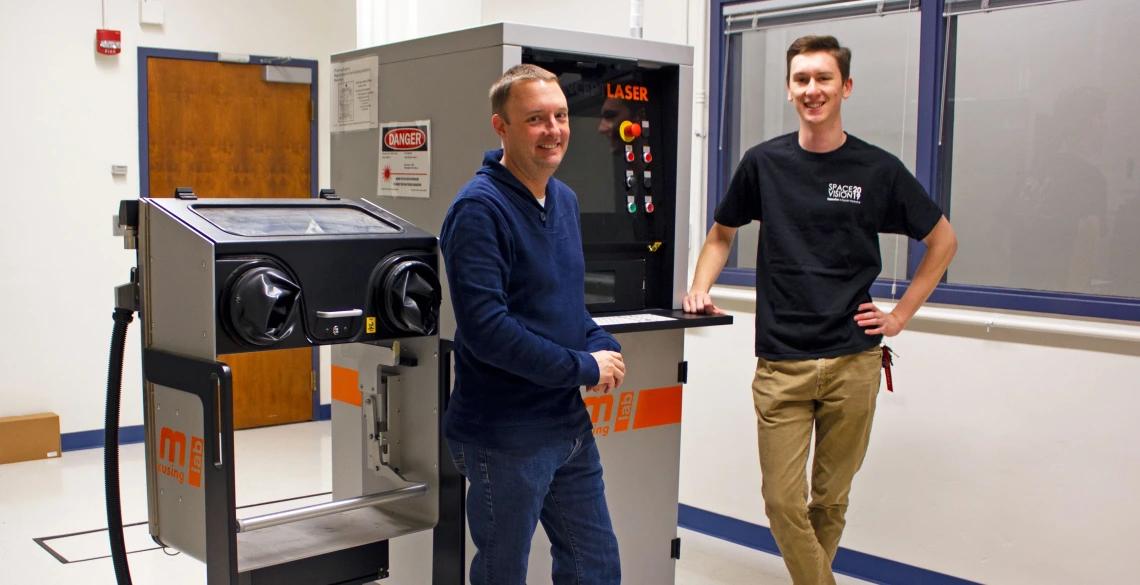
Professor Andrew Wessman and sophomore Daniel McConville, both of the Department of Materials Science and Engineering.
A 3D printer housed in the College of Engineering gives students and researchers across campus a new way to build everything from heat-resistant parts for jet engines to detailed surgical implants and tooling for research projects.
3D printing, also known as additive manufacturing, transforms digital parts designs into physical objects by depositing molten material one layer at a time to harden into a 3D shape. This MLab Cusing 200R model, provided by Honeywell and worth about $400,000, is the first and only machine on campus that uses additive manufacturing to create metal objects.
“Additive manufacturing opens up a freedom for designing new components for aerospace, biomedical and automotive applications that you couldn’t make any other way,” said Andrew Wessman, assistant professor of materials science and engineering, whose lab is housing the equipment. “This machine opens up opportunities for collaborations across the college and across campus -- with optical sciences, architecture and even fine arts.”
The machine, which the Honeywell team nicknamed “Kenobi” after the legendary Jedi master, constructs parts by laser melting metal powders such as stainless steel, nickel alloys and titanium.
Applications Across the Earth -- and Beyond
Applications for additive manufacturing are widespread. For example, it could enable the production of replacement parts for vehicles that are no longer manufactured. Soldiers in remote areas could build equipment parts by melting down spent brass shells, broken or surplus steel parts. They can even use soil, mixed with a binding agent, as a construction material. The use of 3D printing in space exploration is specifically highlighted in the university’s strategic plan. For example, astronauts may someday repurpose regolith, or loose rocky material found on distant planets, to 3D-print replacements for broken spaceship parts.
While many additive manufacturing programs are led by mechanical engineers working to optimize the fabrication process, materials science and engineering researchers are leading the University of Arizona initiative. The department is designing better materials at the outset to produce stronger and more lightweight structures.
“The research we’re doing here will allow people to use the metals more effectively, or to use different kinds of metal alloy,” Wessman said. “We want to identify metal alloys that are really resistant to high temperatures encountered by objects like jet engines or rockets and create better engines that are still printable.”
The machine also opens up new educational opportunities. Wessman will be teaching a metal additive manufacturing course, open to students across campus, beginning in fall 2020.
“This is the first machine in a long family of machines we hope to bring here,” said materials science and engineering department head Pierre Deymier. “This initiative is targeting not just a research program, but also an education program, because students will gain hands-on experience with the machine. In some ways, it’s also a part of a workforce development program in additive manufacturing for the state of Arizona.”
Opportunities for Students
A 2019 report by Reports and Data projects that the additive manufacturing market will reach $23.33 billion in value in 2026, making experience in the field a valuable commodity.
“Honeywell and other U.S. industry players are seeing rapid growth in hiring in additive manufacturing,” said Greg Colvin, a technical fellow at Honeywell Aerospace. “Honeywell provided this equipment to the department to spur innovation, educate students with hands-on experience and help provide a pipeline of engineers and scientists with additive manufacturing experience to industry.”
A group of students working on a 2020 Honeywell-sponsored senior capstone project will be among the first to use the machine. They are creating a custom build plate with temperature control capabilities to investigate how the temperature of the surface on which parts are built affects construction.
“Additive manufacturing is a huge, growing field,” said capstone project team member Ed Buster, a mechanical engineering major. “It’s a tool mechanical engineers are going to need to know in the future.”
Materials science and engineering major Louie Arciniaga is working on the project as well. He has used additive manufacturing in his role as an undergraduate research assistant with John Szivek, a BIO5 faculty member and professor of orthopaedic surgery, aerospace and mechanical engineering, biomedical engineering, materials science and engineering and physiological sciences. One of Szivek’s research projects uses 3D printing to create scaffolding around which broken bones can regrow and heal.
Materials science and engineering doctoral student Anna Hayes used a machine similar to the MLab Cusing 200R during an internship at Phoenix Analysis & Design Technologies, and her master’s thesis focused on additive manufacturing with regolith.
“Because it’s such a new process, there is still a lot that is not understood about the metallurgy and how changing the process can alter the properties of your final part,” she said. “It’s a big area for research, so this machine provides a valuable chance for materials science and engineering students to learn about the solidification process.”