UA Team to 3D-Print Medical Masks
Engineering and health sciences researchers are teaming up to address the shortage of personal protective equipment in Tucson health care facilities.
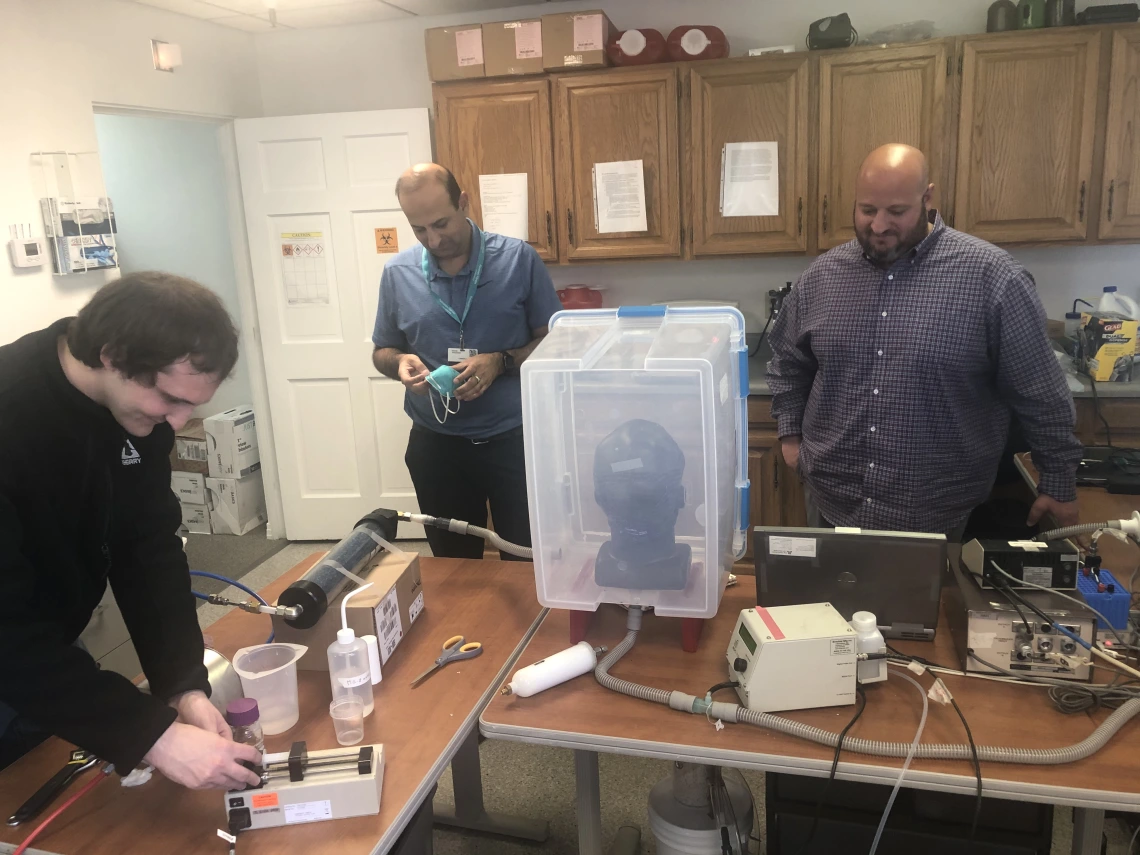
Connor Stahl, a chemical engineering doctoral student; Dr. Sachin Chaudhary, director of the Interstitial Lung Disease Program at Banner - University Medical Center Tucson; and Christopher Morton, research specialist at the College of Medicine, test the efficiency of a 3D-printed mask prototype.
Amid the COVID-19 pandemic, hospitals across the world are running short on personal protective equipment, including N95 respirators – masks that, unlike surgical masks, fit tightly around the face and are capable of filtering out 95% of airborne particles.
In response to the shortage, a group of University of Arizona researchers is working to design, 3D-print and test masks for health care workers in Tucson.
The team includes Doug Loy and Krishna Muralidharan of the Department of Materials Science and Engineering, Sairam Parthasarathy of the Department of Medicine and Armin Sorooshian of the Department of Chemical and Environmental Engineering.
Loy and Muralidharan are working on the design and printing of the masks. Parthasarathy, a medical doctor, and Sorooshian, who studies aerosol particles in the atmosphere, will test how well the masks keep out harmful biological particles, to ensure they meet the standards of the National Institute for Occupational Safety and Health.
"We want to design masks that we can print relatively quickly and make them into a form that people will want to use, so it should wear similarly to the N95 mask," said Loy, who also has a joint appointment in the Department of Chemistry and Biochemistry. "We're finding a lot of designs online that may look good, but they either require the assembly of dozens of parts or they would take forever to print, which drove our decision to take a different approach."
The materials scientists, as well as a group of undergraduate and graduate students, are currently testing out designs and materials for masks using on-campus 3D-printing machines. They're exploring the options of creating reusable masks with disposable filters – similar to anti-pollution bicycle masks – and masks that are entirely permeable to air but not biological materials – like N95 masks.
The College of Engineering and the materials science engineering department provided funding to order 10 new 3D printers, which will allow the team to scale up production to 200 masks and 2,000 disposable filters per week.
"These researchers are developing prototypes that could be printed out in communities all over the world facing medical supply shortages," said David Hahn, Craig M. Berge Dean of the College of Engineering. "We are proud that faculty are working at the intersection of engineering and medicine to rise to the challenge this crisis presents."
With the new 3D printers on their way, the team hopes to start producing masks within the next two weeks. The printers are all equipped with cameras and Wi-Fi control, so the process can be almost entirely automated, allowing researchers to follow physical distancing guidelines. Once they settle on an optimized mask design, they plan to release it to the public so others can print masks as well.
Their work complements efforts by Parthasarathy to build a mask prototype using FDA-approved parts. Producing masks locally, he points out, can help Tucson become self-sufficient and less dependent on external pipelines, many of which cannot keep up with demand.
"They say necessity is the mother of invention," Parthasarathy said. "We have Armin, who can do these sophisticated aerosol measurements, and Doug and Krishna, who have the know-how and the number of students to help create these materials. We've never worked together before, but I think something like this is an example of how there are pockets of support and resident expertise from engineering and health sciences. And now we are coming together to help make this a reality."
If you'd like to contribute to these efforts, you can make a gift to the College of Engineering Biomedical Device Fund.