Two capstone teams help move carpal tunnel syndrome treatment toward market
Project sponsor seeks to launch an accessible product that provides an alternative to surgery.

Students inventing a mechanical brace to treat symptoms of carpal tunnel syndrome admire their prototype, winner of the $2,500 RBC Sargent Aerospace & Defense Voltaire Design Award at the 2024 Craig M. Berge Design Day.
After researching carpal tunnel syndrome for over a decade, Zong-Ming Li has invented a device to relieve symptoms caused by the hand problem. With help from the College of Engineering’s Interdisciplinary Capstone program and Tech Launch Arizona, the professor of biomedical engineering and orthopaedic surgery is on the cusp of making the conservative carpal arch space augmentation mechanism available to patients.
“Carpal tunnel syndrome is a highly prevalent problem, and translating our findings to benefit patients is extremely satisfying,” said Li, also the William and Sylvia Rubin Chair of Orthopaedic Research and associate director of the University of Arizona Arthritis Center.
Li represented capstone sponsors UA College of Medicine – Tucson and the college’s BME department in guiding Teams 24020 and 24021 during the 2023-2024 academic year. The sponsors tasked each student team with taking a different approach to designing and building a prototype to relieve CTS symptoms – including pain, weakness, numbness and tingling – in hands and arms.
CTS results from compression of the median nerve within the carpal tunnel, a narrow passageway on the palm side of the wrist. Both teams’ wearables apply specific forces to manipulate the carpal arch and treat this compression. Team 24020 used mechanical engineering – a precise tightening apparatus and a spring. Team 24021’s invention employs battery-powered electronics controlled by a user interface. Both teams won awards at the 2024 Craig M. Berge Design Day for their year-long projects that completed their University of Arizona degrees as part of the college’s Craig M. Berge Engineering Design Program.
Li is working with TLA, the university’s commercialization arm, to launch a startup to produce over-the-counter CTS braces developed through his many years of research and clinical trials and accelerated by the two capstone teams’ work. The project is featured on StartupHub, a website TLA launched this year to connect UA inventors with entrepreneurs.
Li’s solution is novel in that it targets the median nerve, whereas existing braces only stabilize the wrist. About half a million U.S. patients seek surgery for CTS every year, and surgery is not the solution for everyone, Li said. The Rheumatology Research Foundation estimates that up to 10 million Americans have CTS. That leaves many who don’t choose surgery but also don’t find meaningful relief.
The two projects were Li’s first experience with the Interdisciplinary Capstone program, and he’s pleased with the students’ contributions. He plans to engage another capstone team in the 2024-2025 academic year to further refine and streamline the designs while moving toward commercialization.
“We have proven our concept is sound. Next is finding the most intelligent implementation,” said Li, who is working with TLA to develop the best pathway to market for the device.
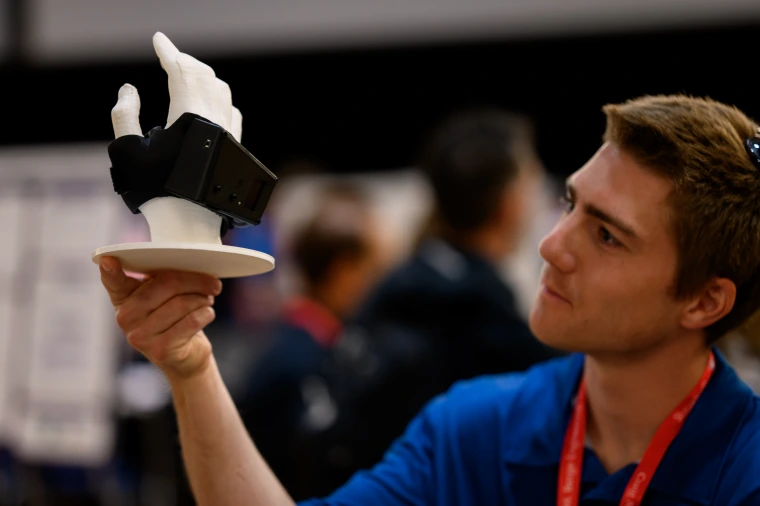
Judge and chemical engineering alum Matt Kingzett checks out Team 24021’s electronically controlled brace at the 2024 Craig M. Berge Design Day. The project won the $1,250 W.L. Gore and Associates Award for Lifelong Innovation. Kingzett works at Gore as a lead engineer.
Training for a helping career
Brandon Bounds was the student procurement lead for Team 24020 before graduating in May with a BME degree. That same month, he started medical school at Texas A&M University in Houston. He plans to concurrently earn a master’s in engineering before beginning his career with the U.S. military, as he is participating in the Health Professions Scholarship Program.
The project was Bounds’ first choice for his capstone.
“I kind of fell in love with how applicable and solution-oriented it is,” said Bounds. “You can help people the same day they put on the brace.”
Bounds is excited by the prospect of his team’s work contributing to a widely available treatment for the millions who suffer from CTS.
Bounds found the project’s hands-on nature beneficial, as well as collaborating with students majoring in other engineering fields. The team created several iterations of a brace before they settled on a final design. When Bounds’ team won the RBC Sargent Aerospace & Defense Voltaire Design Award – for simple, elegant, effective design – they felt recognized for learning not to overcomplicate the product.
Starting over was stressful, he said.
“But looking back, it definitely taught us lessons of how to think through these steps better and to think ahead rather than just kind of plunge straight in and hope it's the best solution.”