Protecting the Pipes Used to Harvest Solar Energy
University of Arizona engineers are using $1M from the DOE to minimize corrosion in large-scale solar energy production.
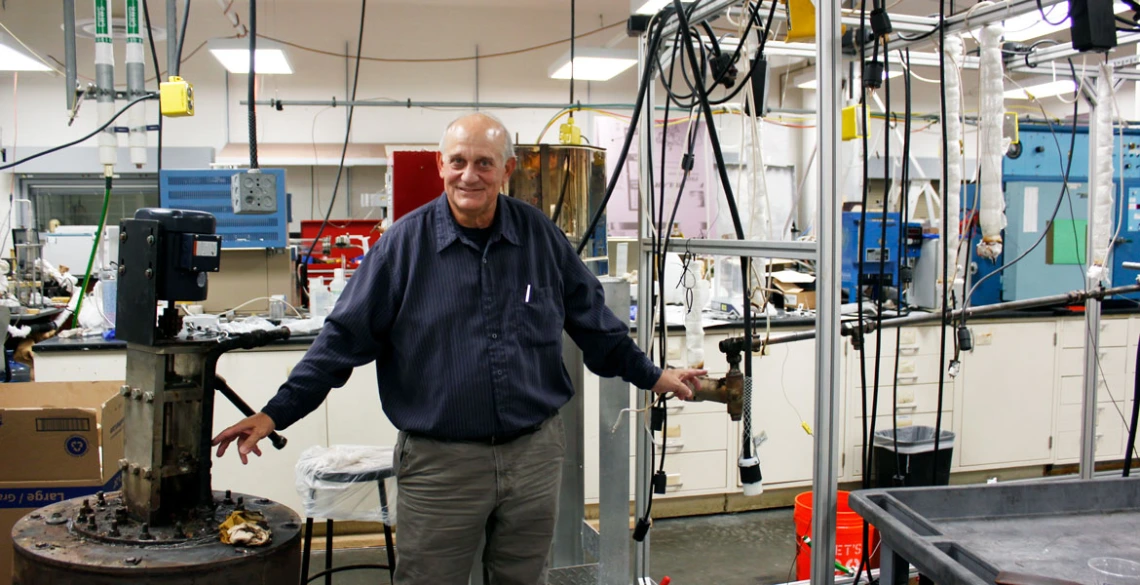
Dominic Gervasio in the lab of his co-primary investigator, Peiwen "Perry" Li, with a pump and a pipe used to research thermal energy.
The advantages of solar power are well documented. The U.S. Office of Energy Efficiency and Renewable Energy projects that meeting 27% of the U.S. electricity demand with solar power by 2050 could eliminate 8 billion metric tons of carbon dioxide from the atmosphere and provide $400 billion in health and environmental benefits across the country.
A team of University of Arizona engineers led by Dominic Gervasio, associate professor of chemical and environmental engineering, is advancing methods for harvesting the power of the sun by detecting and arresting corrosion in the pipes that contain it. A three-year, $1 million grant from the Department of Energy is funding the work.
Gervasio’s co-principal investigators are James Farrell, professor of chemical and environmental engineering and civil and architectural engineering and mechanics, and Peiwen “Perry” Li, department head and professor of aerospace and mechanical engineering.
Solar Power From Salt
Despite their popularity, photovoltaic solar panels aren’t the only way to harness solar power.
A method called concentrating solar power uses the sun to heat a mixture of chloride salts, such as table salt, to about 800 degrees Celsius, which is around 1,500 degrees Fahrenheit. Then, the molten salt travels through a metal pipe to a heat exchanger and heats water on the other side of the exchanger to make steam. The steam spins a turbine, just like in a conventional power plant, to make electricity, all without consuming any coal, oil or natural gas. Because extra molten salt can be produced during the day and stored, this technique makes it possible to generate electricity derived from solar power even at night.
However, when air leaks into these molten chloride salts, oxygen and water enter the mix, and the aerated molten salt mixture can cause the inside of the pipes to corrode, or rust.
“The rusting rates are on the order of microns, or millionths of a meter, per year -- probably lower than 30 microns when there is no water or oxygen in the salt, but can be as high as 3,000 if air leaks into the salt,” Gervasio said. “Even 3,000 microns a year corresponds to a small mass change over the period of a day, but unchecked over weeks, that could pop a hole in the pipe.”
Controlling Voltage
Galvanic corrosion occurs because the electrical potential of the metal in the pipe is more negative than the electrical potential of the oxygen and water. During corrosion, the oxidants -- oxygen and water -- shift the metal’s electrical potential positive, transforming the metal in the pipe to positively charged metal ions. At the same time, the pipe gives away its electrons to the oxygen and water in the molten salt. The more positive the metal potential becomes, the faster the metal corrodes. If there were a way to keep the metal potential negative, then it would not dissolve as metal ions. Well, there is, and Gervasio was on the team that invented it.
Working with Tech Launch Arizona, the office of the UA that commercializes inventions stemming from university research, Gervasio and his colleagues launched a startup called Caltrode in 2016. The company is centered around an invention called a “reference electrode,” which is a sensor that allows technicians to control the electrical potential of a metal pipe.
“By imposing the right voltage, you can make the potential of the metal pipe very negative, and if you make it sufficiently negative, the metal will not corrode,” Gervasio said.
Something’s Gotta Give … Electrons
Without a reference electrode to help control the potential of the pipe, oxygen or water entering through a leak in the pipe causes the metal’s potential to change, so the metal starts corroding as it donates electrons to the water and oxygen. With the reference electrode controlling the electrical potential of the pipe, even though electrons come out of the pipe, the metal doesn’t corrode. What gives? Scientists take advantage of a method called cathodic protection, which makes use of a sacrificial anode. The sacrificial anode is electrically connected to the pipe and has a more negative electrical potential than the metal of the pipe itself. The zinc rod in your water heater is one example of this.
“The pipe wants to send electrons to the water, but the sacrificial anode sends them instead, so it’s the sacrificial anode that rusts instead of the pipe,” Gervasio said.
While cathodic protection has been used on the outside of pipes before, this team will be the first to use this method on the inside of a pipe with molten salts. Their application is also unique. Rather than shorting the sacrificial anode directly to the pipe, as the zinc rod is in a water heater, they’re inserting a power supply between the two, so as the sacrificial anode starts giving away electrons, a current is seen at the power supply, alerting technicians about a leak.
“If there’s a leak in the pipes, we want to know,” Gervasio said “So, this current does two things: It keeps the pipe at the right potential, protecting it from popping a hole, and it’s a signal that there is a leak, so timely corrective action can be taken.”